Nanoscale Additive Manufacturing: Small Particles with Big Potential
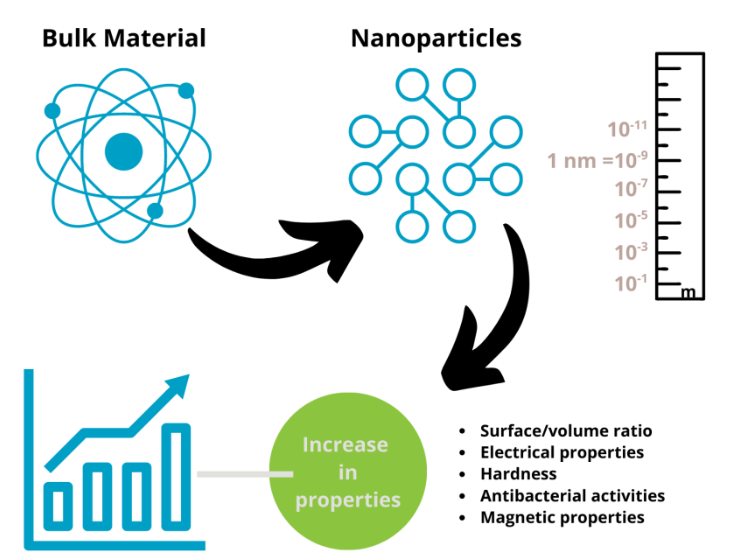
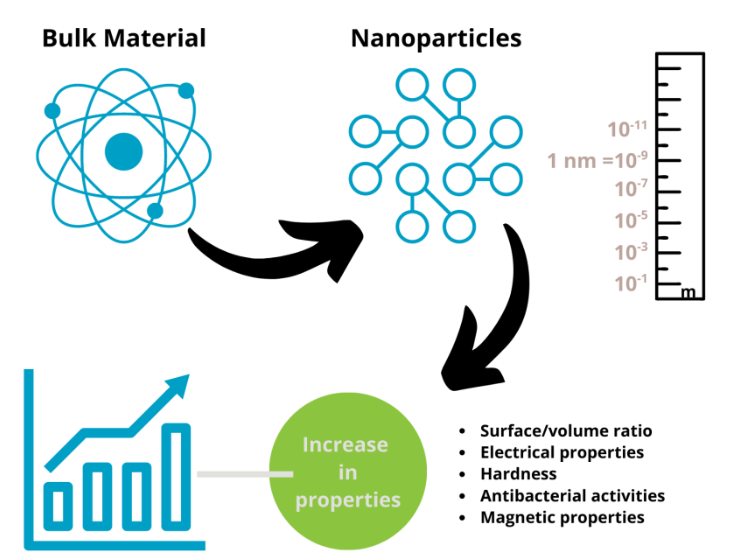
Nanonization and additive manufacturing
Additive manufacturing (AM) is used to rapidly prototype highly-customizable near-net shapes requiring minimal post-processing while using less material than conventional subtractive manufacturing techniques. Typically, the materials used in these processes have been microparticles, but as AM techniques mature, there is increasing interest in using smaller particles to obtain ever-smaller shapes with increased dimensional accuracy.
Different types of nanoscale 3D printing
Various methods have been used to achieve nanoscale precision (feature sizes in the range of 1 – 100 nm) using metal-containing nanomaterials, including friction-stir additive manufacturing, stereolithography, and selective laser sintering.
Benefits of nanonization for additive manufacturing
For years, material scientists have shown that decreasing a material’s size to the nanoscale can cause novel material properties to emerge that are not observed at larger size scales. Compared with using microparticles (e.g., -53/+15 μm or -65/+20 μm), using nanoparticles offers advantages for various applications, typically due to an increase in the volume-to-surface ratio. Many industries, including additive manufacturing, are increasingly interested in 3D printing techniques that can obtain materials requiring nanoscale precision.
For additive manufacturing, the addition of nanoparticles can provide several advantages:
- Enhanced laser absorption1
- Increased final part density
- Improved mechanical properties such as hardness2,3
- Lower sintering temperatures4
- Improved surface finish5
- Improved energy efficiency and faster laser processing6
How does nanonization improve properties?
The use of smaller particles has been shown to increase the density of final parts while using a faster scanning speed—helping maintain product quality while decreasing fabrication time.
Because post-processing can be time-consuming and expensive, using an appropriate feed material can help ensure that a formed part is of the desired quality.
A densely packed powder bed can be critical to maximizing the density and uniformity of the final part obtained by additive manufacturing. One of the most important factors affecting the performance of a 3D-printed piece is the particle size distribution. The relationship between particle size distribution and final product properties is complex,7 but research has shown that using a mixture of large and small particles in a powder can help fill in the gaps between larger particles, which increases the packing density. In laser-based AM techniques, using a bimodal distribution can increase the powder packing and the amount of laser energy absorbed by the bed.
Reade’s 3D Printing Powders
Although many of these additive manufacturing techniques are still in the research and development stage, Reade is thrilled to partner with national labs and leading universities around the world, including Lawrence Livermore National Laboratory, Massachusetts Institute of Technology, Auburn University, Drexel University, Ohio State, and Stellenbosch University. Our powders have recently been used in several academic publications for laser direct energy deposition to obtain advanced alloys.8,9
Including nanoparticles in metal powder formulations can increase the properties of the final parts, but particle size reduction is a complex process that requires special expertise and equipment. By partnering with Reade and our team of experts, you can take full advantage of our range of gas-atomized metal and ceramic powders for 3D printing, including aluminum, cobalt, iron, nickel, silver, stainless steel, titanium, and tool steel.
If you want to use metal nanoparticles for your additive manufacturing process, please contact Reade to discuss your specific requirements.
References
(1) Aluminum with dispersed nanoparticles by laser additive manufacturing | Nature Communications. https://www.nature.com/articles/s41467-019-12047-2 (accessed 2023-02-08).
(2) Tan, Z.; Li, J.; Zhang, Z. Experimental and Numerical Studies on Fabrication of Nanoparticle Reinforced Aluminum Matrix Composites by Friction Stir Additive Manufacturing. J. Mater. Res. Technol. 2021, 12, 1898–1912. https://doi.org/10.1016/j.jmrt.2021.04.004.
(3) Sehrt, J. T.; Kleszczynski, S.; Notthoff, C. Nanoparticle Improved Metal Materials for Additive Manufacturing. Prog. Addit. Manuf. 2017, 2 (4), 179–191. https://doi.org/10.1007/s40964-017-0028-9.
(4) Sharif, A.; Farid, N.; O’Connor, G. M. Ultrashort Laser Sintering of Metal Nanoparticles: A Review. Results Eng. 2022, 16, 100731. https://doi.org/10.1016/j.rineng.2022.100731.
(5) Lim, H.; Khan, N. A. EFFECTS OF PARTICLE SIZE DISTRIBUTION ON SURFACE FINISH OF
SELECTIVE LASER MELTING PARTS.
(6) Qu, M.; Guo, Q.; Escano, L. I.; Nabaa, A.; Fezzaa, K.; Chen, L. Nanoparticle-Enabled Increase of Energy Efficiency during Laser Metal Additive Manufacturing. Addit. Manuf. 2022, 60, 103242. https://doi.org/10.1016/j.addma.2022.103242.
(7) Averardi, A.; Cola, C.; Zeltmann, S. E.; Gupta, N. Effect of Particle Size Distribution on the Packing of Powder Beds: A Critical Discussion Relevant to Additive Manufacturing. Mater. Today Commun. 2020, 24, 100964. https://doi.org/10.1016/j.mt-comm.2020.100964.
(8) Pan, Q.; Kapoor, M.; Mileski, S.; Carsley, J.; Lou, X. Technical Basis of Using Laser Direct Energy Deposition as a High-Throughput Combinatorial Method for DC-Cast Al-Mn Alloy Development. Mater. Des. 2021, 212, 110290. https://doi.org/10.1016/j.mat-des.2021.110290.
(9) Pan, Q.; Kapoor, M.; Mileski, S.; Carsley, J.; Lou, X. Phase Transformation and Micro-
structure Evolution of AA3104 Alloy Made by Laser Additive Manufacturing. In Light Met-
als 2022; Eskin, D., Ed.; The Minerals, Metals & Materials Series; Springer International
Publishing: Cham, 2022; pp 179–185. https://doi.org/10.1007/978-3-030-92529-1_24.