Innovations in Battery Recycling: Paving the Way for Sustainable Energy Storage
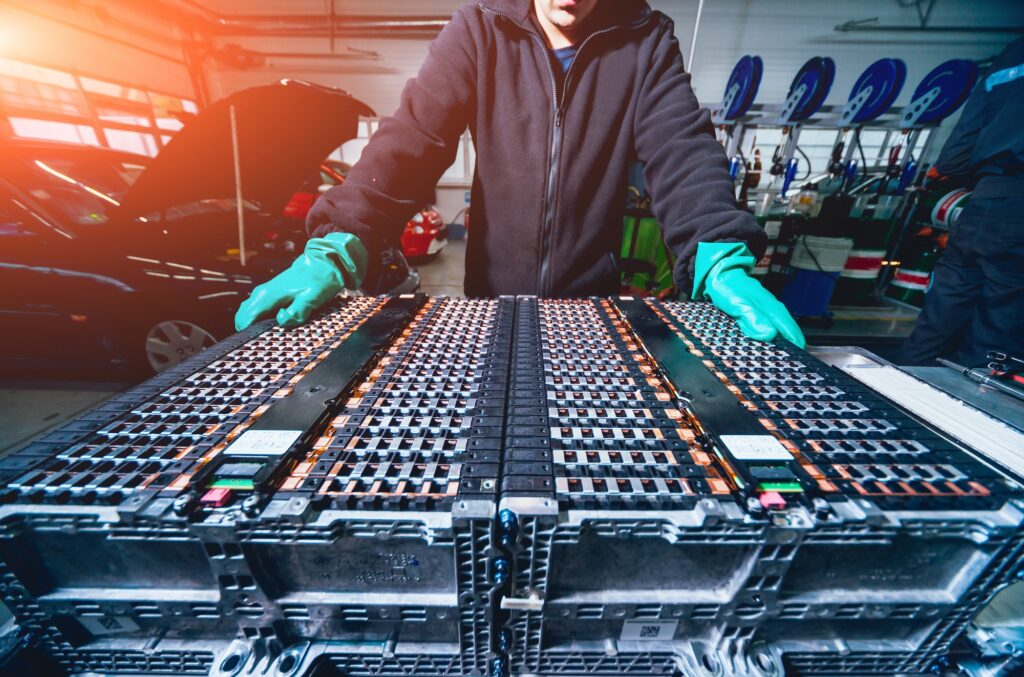
As the global shift toward cleaner energy picks up speed, lithium-ion batteries (LiBs) have become the driving force behind electric vehicles, portable electronics, and renewable energy storage. These versatile, high-performance batteries promise to reduce carbon emissions and foster a more sustainable future. However, with LiB usage on the rise, the question of how to recycle them effectively at the end of their life cycle becomes urgent. This blog post examines recent breakthroughs in LiB recycling, highlights hydrometallurgical and direct recycling processes, and explores closed-loop systems that minimize environmental impact. We at Reade also discuss how our expertise in advanced materials can help create a more sustainable material cycle.
The Growing Need for Lithium-Ion Battery Recycling
LiBs contain valuable metals like lithium, cobalt, nickel, and manganese—many of which are finite resources. A study in Nature (Harper et al., 2019) suggests that well-planned recycling can recover the bulk of these materials, saving energy and reducing landfill waste. Yet traditional recycling methods often face high costs, limited metal recovery rates, and environmental risks. Recent innovations aim to overcome these hurdles by refining chemical processes, enhancing automation, and adopting more eco-friendly solvents to optimize recovery rates and reduce waste. As battery technology continues to evolve, effective recycling strategies have become essential to ensuring sustainable growth for the entire energy sector.
Hydrometallurgical Processes: A Key Innovation
Hydrometallurgical recycling dissolves battery metals in aqueous solutions (usually acids). From here, metals such as lithium, cobalt, and nickel can be precipitated or extracted for reuse. Advances in acid leaching have improved metal recovery efficiency (Zeng, Li, & Singh, 2014). Meanwhile, streamlined processes, including automation and “green” solvents, help reduce energy costs and cut hazardous waste. Because hydrometallurgical methods can also be adapted to different battery chemistries, they offer a versatile path toward higher throughput and cleaner production cycles.
Direct Recycling: Preserving Battery Components
Whereas hydrometallurgical recycling breaks batteries down into base metals, direct recycling seeks to preserve functional components—especially the cathode. Relithiation techniques allow spent cathodes to be replenished with lithium and reused in new batteries (Zhang et al., 2021). This method uses less energy than metal extraction and can lower costs further. However, direct recycling requires careful sorting by chemistry, degradation level, and contamination to ensure consistent performance. When executed effectively, direct recycling helps retain the integrity of battery materials, contributing to a circular model where fewer resources are wasted.
Towards a Closed-Loop System
A closed-loop approach envisions LiBs manufactured, used, collected, and recycled, with recovered materials returning to production. In this cycle, reliance on virgin resources drops, cutting mining and refining impacts. As technologies improve, recovered cobalt and lithium can meet a growing share of demand, minimizing supply chain instability. In addition, lifecycle assessments show that robust recycling efforts can significantly reduce the carbon footprint of LiBs (Dunn et al., 2012). Collaboration among manufacturers, recyclers, policymakers, and suppliers is crucial to standardize collection and recycling protocols. By establishing guidelines for battery handling, storage, and transport, the industry can ensure that valuable materials are not lost and environmental harm is minimized.
Reade’s Role in Advancing Sustainable Solutions
At Reade, we have specialized in advanced materials since 1773, providing technical expertise, in-depth research, and a vast network of resources. Our decades of experience in raw materials—ranging from metals and minerals to high-purity chemicals—enable us to guide partners toward effective processes for recovering critical metals. We collaborate with battery manufacturers, and research institutions to streamline the flow of reclaimed components into new batteries.
Whether sourcing virgin or recycled materials, we maintain strict quality standards—ensuring reliability when integrating reclaimed metals into new LiB products. Our mission includes fostering sustainable partnerships that not only reduce waste but also lower environmental impacts across multiple industries. By bridging the gaps between key stakeholders, we help transform recycling challenges into viable, cost-effective opportunities.
Future Outlook
Emerging battery recycling methods, particularly hydrometallurgical and direct recycling processes, are steering energy storage toward efficiency and sustainability. With ongoing technological advancements and increased support from policymakers, closed-loop models are poised to become the industry standard. This shift promises not only to conserve valuable raw materials but also to alleviate the environmental challenges tied to mining and disposal. As battery demand continues to surge—driven by electric mobility and renewable energy expansion—our commitment at Reade remains focused on bridging gaps between manufacturers, recyclers, and raw material suppliers. By optimizing recycling systems, promoting best practices, and championing a truly circular economy, we can help ensure a cleaner, more resilient energy future for all.
References
- Dunn, J. B., Gaines, L., Kelly, J. C., James, C., & Gallagher, K. G. (2012). The significance of Li-ion batteries in electric vehicle life-cycle energy and emissions and recycling’s role in its reduction. Energy & Environmental Science, 5(3), 3972-3983.
- Gaines, L. (2018). The future of automotive lithium-ion battery recycling: Charting a sustainable course. Sustainable Materials and Technologies, 17, e00068.
- Harper, G., Sommerville, R., Kendrick, E., Driscoll, L., Slater, P., Stolkin, R., … & Anderson, P. (2019). Recycling lithium-ion batteries from electric vehicles. Nature, 575(7781), 75–86.
- Zeng, X., Li, J., & Singh, N. (2014). Recycling of spent lithium-ion battery: A critical review. Critical Reviews in Environmental Science and Technology, 44(10), 1129–1165.
- Zhang, W., He, Y., Zhao, H., & Li, J. (2021). Relithiation strategies of spent lithium-ion battery cathodes for direct recycling: A critical review. Renewable and Sustainable Energy Reviews, 141, 110777.