Electrochemical Deposition for Next-Gen Metal Recovery and Manufacturing
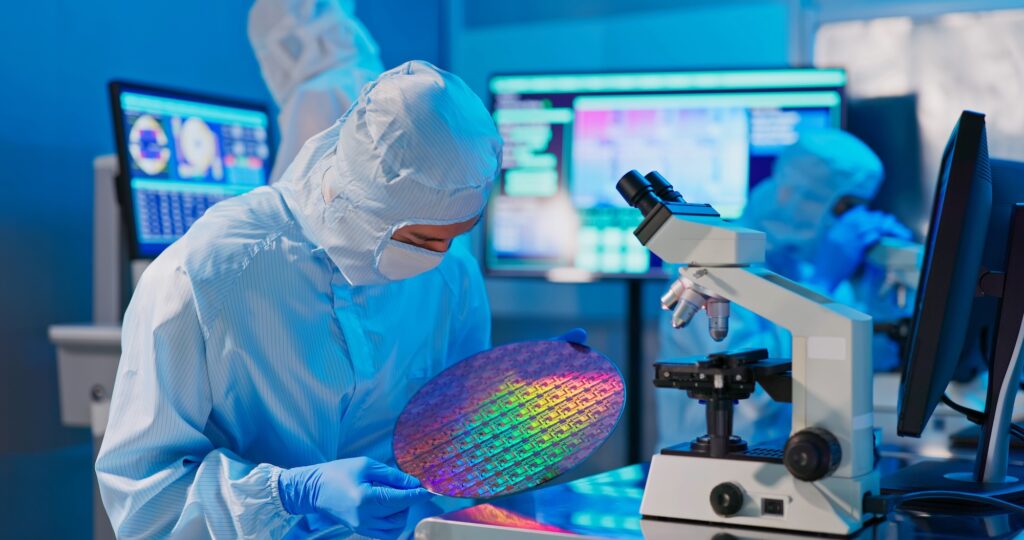
Electrochemical deposition, often referred to simply as electrodeposition, is a versatile process that has been used for decades to extract, purify, and refine metals. Today, as industries strive for more sustainable solutions, electrodeposition is undergoing a surge in innovation, offering a green pathway toward advanced metal recovery and manufacturing. From rechargeable batteries and aerospace components to semiconductor applications, this technology has broad potential to revolutionize how we source critical metals and build high-performance products. Below, we unpack the science behind electrodeposition, explore recent optimizations that reduce environmental impact, and discuss real-world uses in cutting-edge industries. We also highlight how we at Reade, with our depth of expertise in advanced materials, play a key supporting role for businesses seeking reliable solutions in this rapidly evolving field.
Fundamentals of Electrochemical Deposition
Electrodeposition involves passing an electric current through an electrolyte solution containing dissolved metal ions. Metal cations migrate to the cathode (a negatively charged electrode), where they gain electrons and deposit as a solid metal layer. Conversely, oxidation occurs at the anode (positively charged electrode), driving the overall electrochemical reactions necessary for the process.
- Key Parameters
- Solution Chemistry: The composition of the electrolyte (including pH, concentration, additives, etc.) greatly influences deposit morphology, purity, and efficiency.
- Electrode Material: Different electrode substrates (e.g., copper, nickel, stainless steel) can alter the deposition rate and final metal structure.
- Temperature and Current Density: These variables affect how fast metal ions reduce and how uniform the metal coating or recovered metal becomes.
- Advantages
- Selective Deposition: By carefully tuning voltage and solution chemistry, different metals can be selectively extracted from multi-metal solutions.
- High Purity: Properly optimized electrodeposition can yield metals that are 99.9% pure or higher, making them ready for high-performance applications (Yang et al., 2019).
- Scalability: The process is adaptable from small-scale lab setups to large industrial lines, offering flexibility for diverse production volumes.
Optimizing for Sustainable Metallurgy
In an era where sustainability is paramount, electrodeposition stands out as an eco-friendly alternative to some traditional metallurgical processes like smelting or pyrometallurgy. Here’s how:
- Reduced Energy Consumption
Processes like pyrometallurgy can require extremely high temperatures, translating into substantial energy usage and greenhouse gas emissions. Electrodeposition, on the other hand, typically operates at relatively mild temperatures. With proper system design, such as using efficient rectifiers and renewable-powered electricity sources, overall energy consumption can be significantly reduced (Tan et al., 2020). - Lower Chemical Waste
Hydrometallurgical methods, while widely used, can generate considerable chemical by-products if not carefully managed. Electrodeposition can help minimize waste by operating in closed-loop systems, where electrolyte solutions are regenerated or reused after metals have been recovered. - Recycling-Friendly Approach
Electrodeposition aligns seamlessly with circular economy principles. Spent solutions can often be treated, refreshed, and used repeatedly. Moreover, electrodeposition can extract high-purity metals from industrial wastewater or e-waste streams, reclaiming valuable materials that might otherwise end up in landfills (Evans & Chen, 2017). - Advanced Control Systems
Modern processes use inline monitoring, sensors, and automated control algorithms. By tracking parameters in real time, engineers can maintain tight control over electrodeposition conditions, thereby minimizing reagent usage and ensuring more precise recovery rates.
Applications Across High-Value Industries
- Semiconductor Manufacturing
The semiconductor industry demands ultrapure metals for fabricating microelectronic components. Copper electrodeposition, for instance, is crucial to creating interconnects in integrated circuits (ICs). Fine-tuning plating baths and current densities allows for uniform copper layers on silicon wafers. Researchers are also examining electrodeposited cobalt, nickel, and other metals to reduce electromigration and improve chip performance (Kang & Hu, 2019). - Aerospace and Defense
In aerospace applications, lightweight yet durable coatings are essential for components exposed to extreme conditions. Electroplated alloys such as nickel-cobalt offer high corrosion resistance and can withstand substantial mechanical stress. Advances in this domain focus on creating nanocrystalline layers that enhance material properties like wear resistance and fatigue strength. - Green Energy Solutions
As renewable energy systems expand, the need for efficient metal recovery grows. Electrodeposition can extract critical metals like lithium, cobalt, and nickel from spent batteries—helping to close the loop on energy storage. Additionally, specialized electrodeposited coatings can improve the efficiency and durability of solar cells, fuel cells, and other emerging green technologies (Lee et al., 2021). - Additive Manufacturing Integration
Electrodeposition isn’t limited to producing flat coatings. Innovative 3D electroplating methods now enable metal patterning for complex, high-value parts, bridging the gap between traditional plating and additive manufacturing. By coupling electrodeposition with advanced masking, lithographic, or laser-direct structuring techniques, manufacturers can build intricate components layer by layer.
We at Reade: Driving Progress in Advanced Materials
Since our founding in 1773, Reade has evolved into a premier resource for specialty chemical solids, metals, and advanced materials. Our deep experience with metal powders, plating salts, and catalysts positions us to support the nuanced demands of electrodeposition processes. We collaborate with manufacturers, research institutions, and supply-chain partners to ensure high-quality raw materials consistently reach our clients.
- Consulting and Technical Expertise: Drawing on decades of hands-on experience, we guide clients through selecting the appropriate metal precursors, bath additives, and purity levels. This tailored approach helps companies optimize their electrodeposition setups quickly and cost-effectively.
- Reliable Sourcing: Our global network allows us to offer a wide range of metals—from common base metals like copper and nickel to more specialized elements such as cobalt and rare alloys. We maintain stringent quality standards, ensuring product consistency and performance across multiple industries.
- Sustainability Partnerships: As more organizations focus on green manufacturing, we help align material sourcing strategies with closed-loop aspirations. By identifying suitable recyclers or plating bath regenerators, we connect stakeholders, fostering a circular ecosystem for critical metals.
Future Outlook: Evolving Toward a Circular Economy
Electrochemical deposition is more than a simple metal plating process; it’s a dynamic, evolving field set to tackle some of the most pressing material challenges in modern industry. By refining and integrating electrodeposition techniques, stakeholders can benefit from reduced environmental impact, cost savings, and greater supply security of critical metals. The ongoing shift toward electric vehicles, renewable energy, and miniaturized electronics will only increase the relevance of advanced metal recovery and manufacturing approaches.
At Reade, we remain committed to helping businesses harness electrodeposition’s full potential. Whether you’re looking to scale up a metal recovery project, improve product quality in semiconductor fabrication, or explore new alloys in aerospace, our seasoned team offers the technical knowledge and global reach to drive progress. By combining the right raw materials with cutting-edge process design, we can forge a more sustainable path for industries worldwide.
References
- Evans, R. D., & Chen, M. (2017). Recovery of metallic resources from e-waste and wastewater using electrodeposition: A review. Electrochimica Acta, 234, 1–14.
- Kang, S., & Hu, C. (2019). Advanced copper interconnects: Electrodeposition and reliability. Microelectronic Engineering, 215, 110978.
- Lee, J., Patel, A., & Zheng, H. (2021). Electrodeposited coatings for energy-related applications. Progress in Materials Science, 117, 100740.
- Tan, L., Zhang, X., & Liu, Y. (2020). Sustainable electrodeposition processes for metal recovery. Chemical Engineering Journal, 396, 125161.
- Yang, B., Wu, Q., & Sun, S. (2019). High-purity metal deposition: New insights into electrodeposition. Journal of the Electrochemical Society, 166(12), D3057–D3062.